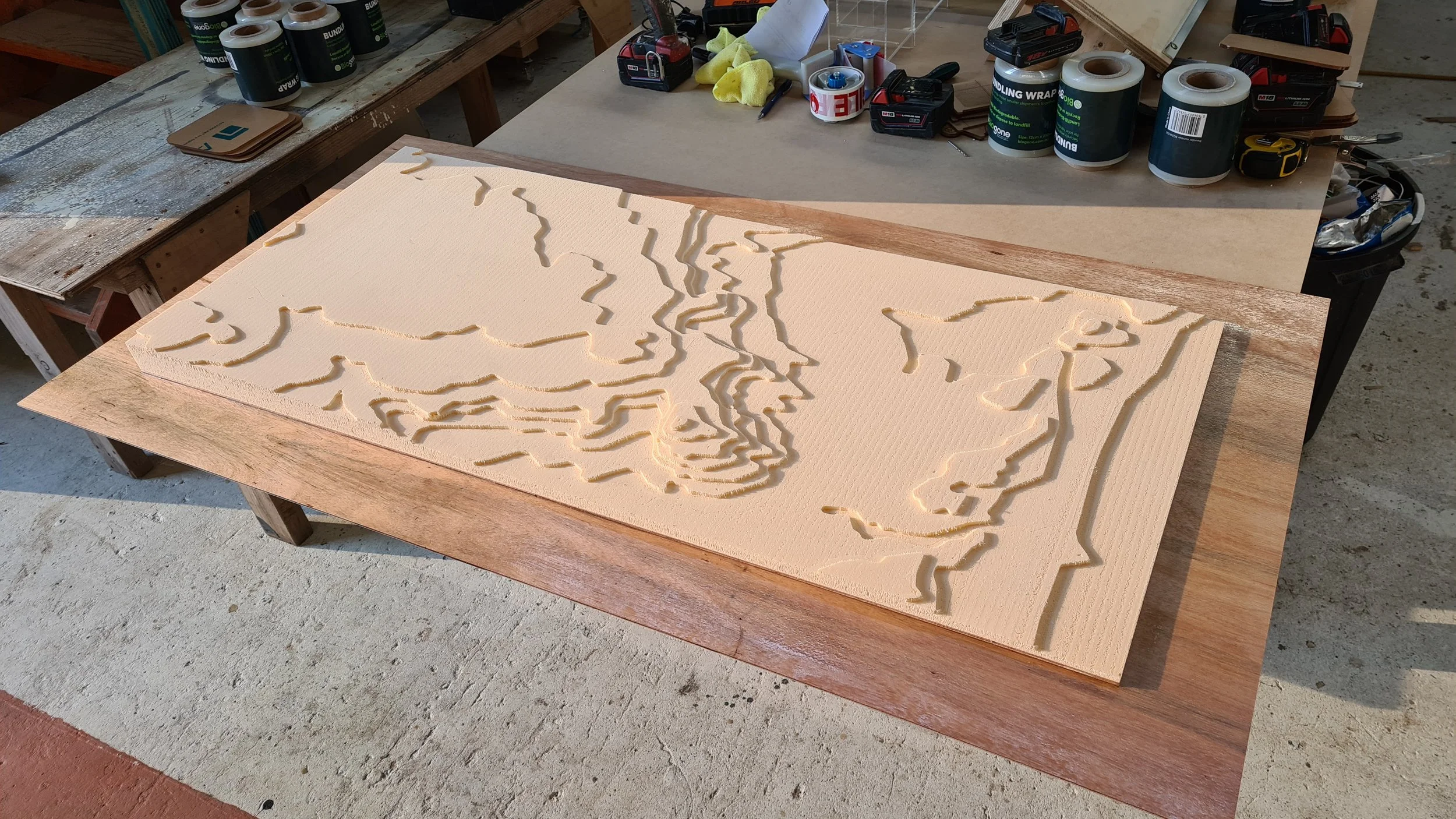
Technical Specifications
Explore the technical details of our CNC routing services. Here, you’ll find comprehensive information about the materials we work with, our machine capabilities, and the precision we bring to every project. For any additional questions, please refer to our FAQ or contact us directly.
Materials We Cut:
We work with a wide range of materials to ensure your project needs are met with the highest quality and precision."
Timber: Plywoods, solid timber, chipboard, MDF (Medium Density Fiberboard)
Plastics: Acrylic, acetyl, nylon, HDPE (High-Density Polyethylene), PVC (Polyvinyl Chloride), Polycarbonate, PETG (Polyethylene Terephthalate Glycol)
Metals: Aluminium (soft metals only)
Composite Materials: ACM (Aluminium Composite Material), Fiberglass, Fibreglass Composites
Others: Foam, cork, cardboard, Acoustic Sheets and various other materials
File Formats:
We accept a variety of file formats to ensure your designs are accurately translated into CNC-ready parts.
Preferred Format: DXF or DWG
Other Formats: DXF, DWG, AI, EPS, PDF
3D Models: STL, STEP, IGES, 3DM (Rhino3D)
Machine Capabilities:
Our advanced CNC machinery ensures precision and efficiency in every cut.
Maximum Sheet Size: 2500mm x 1250mm x 150mm
Machine Travel: 3 axis, XYZ with high precision
Tolerance: +/- 0.1 mm
Router Bits: Various types for different materials and cutting needs.
RPM and Feed Rate: Customizable for optimal cutting performance, 8,0000 to 18,000 rpm and up to 50,000 mm/min.
Depth of Cut: Adjustable based on project requirements and router bits used. Z maximum is 300mm.
Additional Services:
Beyond cutting, we offer several additional services to support your project from start to finish."
Design Assistance: Help with preparing and refining your CAD files
Material Sourcing: High-quality materials procured and ready for cutting
Component Assembly: Partial or complete project builds as needed
Our Tooling Notes:
Keep in mind:
The larger the bit, the faster and deeper the cut, which means cheaper cuts.
The smaller the bit, the slower and shallower the cut, which means more time is required to cut.
Panel Work:
Stock Thickness 0.5-12mm: The standard bit size for this range is a 6.0mm compression bit. We require a minimum part spacing of 7.0mm for this bit with a 10.0mm sheet margin. If more detail is required, we can use smaller bits.
Stock Thickness 12-40mm: For most panel cutting tasks within this thickness range, we use a 9.5mm diameter compression cutter. We maintain 10.0mm part spacing and a 10.0mm margin around the sheet to ensure precise and clean cuts.
Thin Cutters for up to 25mm Stock: For through-cutting 25.0mm thick stock, we use a minimum cutter diameter of 6.0mm. This size allows for intricate and detailed cuts but will take more time to do so.
Sheet Size: When nesting your sheets, be sure to double-check the material size. Some sheets are from 2400mm x 1200mm to 2500mm x 1250mm.
Engraving Depth: We can engrave materials up to a maximum thickness of approximately 150mm, allowing for larger objects to be engraved.
Through Cutting Depth: We can perform through cutting on materials up to 50-60mm thick, suitable for a variety of robust applications. This will require larger bits meaning less detail is possible.
Material Specifics:
Aluminium (1-20mm): For cutting aluminium sheets ranging from 1mm to 20mm in thickness, we commonly use a 6.00mm diameter cutter, ensuring smooth and precise cuts.
Acrylic (3-12mm): For hard plastic materials, 4.0mm or 6.0mm diameter cutter is preferred, providing clean edges and high precision for thicknesses between 3mm and 12mm.
Acoustic, Cloth or Soft Foam s(0.5 to 10.0): We can run drag knife operations of material up to 10mm in thickness. We can cut materials that are usually unable to be cut with a router bit. This uses a blade to use so there is no diameter for these cuts.
Rigid Foams (0.5 to 80mm): We can cut to a maximum of 80mm with specialised foam routing bits. They have a diameter of 8.0mm or 12.0mm.
Tips for Optimal CNC Routing:
Achieving the best results in CNC routing requires attention to detail and careful planning. Here are some tips to ensure your project is a success:
Detail and Router Bit Size: The more detailed the component, the smaller the router bit needed. Smaller bits allow for finer detail but require slower travel speeds and shallower cuts to maintain precision.
Travel Speed and Cutting Depth: Adjusting the travel speed and cutting depth is crucial for achieving high-quality cuts. Slower speeds or shallower cuts help prevent material burn and bit breakage.
Material Choice: Selecting the right material for your project can impact the cutting process. Softer materials may require different bit types and cutting speeds compared to harder materials.
File Preparation: Ensure your design files are clean and well-prepared. Avoid unnecessary complexity in your CAD files to streamline the CAM process. You can nest your own sheets or have us nest them for you.
Toolpath Planning: Efficient toolpath planning can save time and reduce wear on tools. Plan your cuts to minimize tool changes and travel distance.
Time Management: As the saying goes, "time is money." Balancing detail with efficiency is key. More intricate designs will take longer to cut, so plan accordingly to stay within budget.